How to modernize your warehouse with the latest software system?
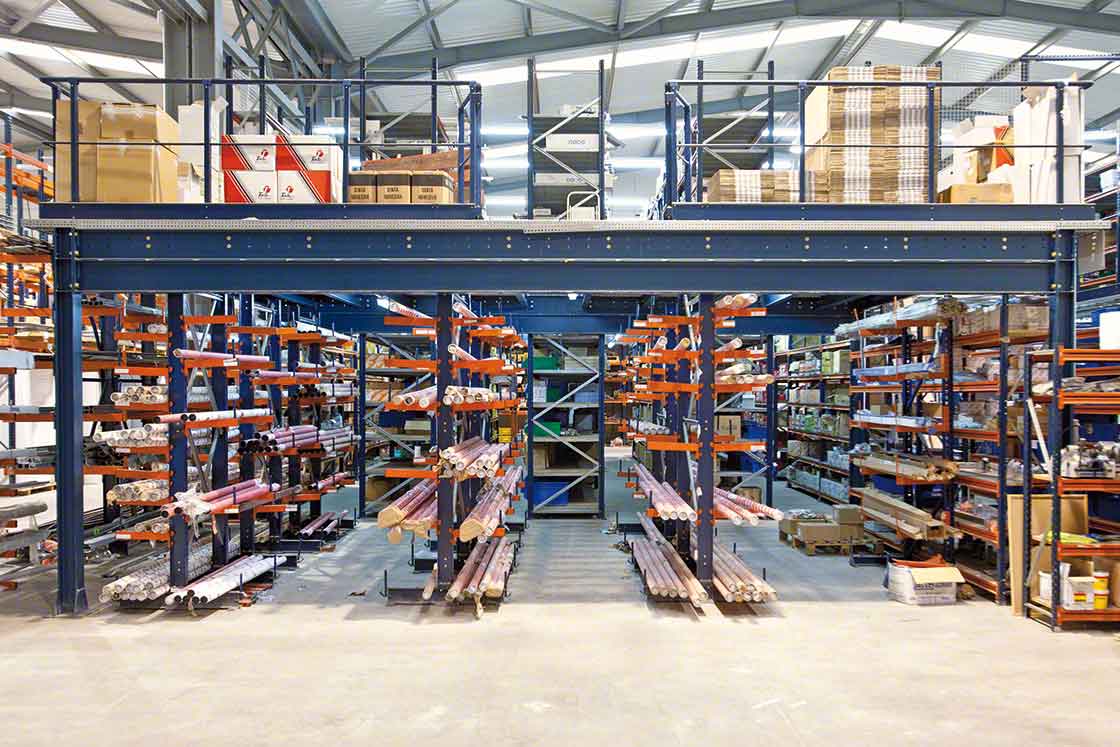
The present degree of optimization is one of the most important aspects in evaluating whether your warehouse will be able to react to changes in technology. The supply chain is continuously changing, therefore it’s critical to make sure your warehouse Singapore not only meets but also exceeds expectations.
That’s why you’re going to discover today how to modernize your warehouse in five simple stages using a warehouse management system.
How has the management of warehousing changed?
E-commerce has mostly replaced traditional brick-and-mortar retail during the previous two decades. As a result, several distribution facilities and warehouses have undergone considerable renovations to better serve customers. Because it may now impact the whole supply chain, warehouse management has also become significantly more difficult. The demand for your warehouse company in Singapore may have increased dramatically recently as a result of items being created and bought by customers around the clock from all across the nation or the world.
You should be able to satisfy this demand if your warehouse has been updated with the most recent technology, including enterprise resource planning (ERP) systems, barcode and RFID scanning, and warehouse management systems (WMS). Stability and growth depend on software. You may start eradicating human error, stock-outs, and other frequent issues warehouses confront by utilizing the latest advancements that are entering the market.
Making use of automatic data collection:
What is the worst thing you can do to your business? When they might merely be scanning barcodes or RFID tags, people instead choose to scribble notes on paper or type long passages of text. This is particularly true when 40,000 goods are dispersed throughout many places. You may start using automated data gathering to automate procedures and increase efficiency after you have a warehouse management system. Because your employees may remove unnecessary and time-consuming duties, you can also reduce labor expenditures.
Simply said, depending on human data entry these days is a grave error. Your WMS can be updated by mobile scanners upon arrival and departure. This eliminates the possibility of identification and counting mistakes.
Modify the layout of your warehouse:
Despite the extensive use of technology, many warehouses across the nation are out-of-date and under-optimized. Why? because they always employ the same warehouse configuration. Your warehouse’s layout must be taken into account when modernizing it. The good news is that, depending on how your warehouse is set up, your WMS can show you the most effective picking paths. The information gathered can also be used to determine whether objects belong in the packaging area.
You should also think about how your warehouse interferes with both machines and humans. Forklifts should be able to operate in the aisles, and the bins and lots should be clearly labeled to guide pickers to the appropriate spot. Popular seasonal goods can be altered at any time of the year. Place an item higher on the shelf as demand declines, for instance.
Data synchronization between all systems:
A separate operation of many systems can quickly make your warehouse dated and lead to unpleasant data silos. Many WMS are adaptable solutions that can be connected to other systems, including ERPs like SAP Business One, and WiSys’ Agility. You specifically wish to synchronize any item’s SKU-related data. Visibility and openness across the supply chain are ensured by standardizing common product data throughout the system and facilities.
Accurate inventory counts also depend on synchronizing data, especially if you run both a physical store and an online business. Giving customers a realistic estimate of what is still available will increase their pleasure more than forcing them to buy something that is out of stock or unavailable.
Ordering Sequences Using Your WMS:
The majority of order processing cycles are very inefficient. According to data from a distribution operations investigation, the majority of orders receive attention for 37.9% of the whole order cycle. 56.1% of the lost time was accounted for by such orders. Workers waiting for lift equipment, clogged isles, things arranged incorrectly, disturbances, stock-outs, and other factors contributed to 6% of the lost time. Although extremely ineffective, a WMS can help.
Your team’s pick pathways may be the cause of their slow order completion and delivery onto the appropriate vehicle. Along with improving your warehouse layout, you should place pickers and packers in the most sensible configurations.
Agility Essentials is one of several warehouse management solutions that let you organize picking routes around the warehouse and order your orders. By grouping lanes together, allocating teams to zones, and even reducing the time required for non-conveyable commodities, you may implement tactics that increase speed and efficiency.
Going Mobile
Are you sick and weary of being connected to desktop computers? Your warehouse management system and other applications, such as mobile POS, may be transferred to mobile management devices. Utilizing tablets and smartphones not only makes scanning, tracking, and planning simpler, but also allows your staff a method to interact more swiftly. It is also made simpler to track their performance.
There is no excuse not to deploy mobile technology in the warehouse nowadays, especially if you process thousands of orders each day.
Conclusion:
The primary goal of contemporary warehousing hasn’t altered despite recent major evolution and increased reliance on technology. After the production process is finished and before the items are transported to other facilities and retail locations, they are stored in warehouses. Before sending their stock to store shelves and floor-level displays, retailers rely on warehouses to keep their goods safe.